Πριν από λίγους μήνες, το Renault Group ανακοίνωνε «ένα ακόμη βήμα προς τον ψηφιακό του μετασχηματισμό, παρουσιάζοντας το πρώτο του βιομηχανικό Metaverse», το οποίο, σύμφωνα με τους υπολογισμούς των Γάλλων, μέχρι το 2025 θα αποφέρει οικονομικό όφελος της τάξης των 320 εκατομμυρίων ευρώ. Επρόκειτο για ένα λογικά αναμενόμενο επεισόδιο στο σήριαλ που ονομάζεται Industry 4.0 και σηματοδοτεί την είσοδο της παραγωγής αυτοκινήτων στην ψηφιακή εποχή.
Είναι μια διαδρομή στην οποία συναντάμε τα ευφυή γυαλιά “google glass” που φόρεσαν για πρώτη φορά το 2014 οι εργαζόμενοι της BMW στο εργοστάσιο του Spartanburg στις ΗΠΑ για τη διενέργεια ελέγχων και δοκιμών σε οχήματα, το Smart Tag System για την παρακολούθηση της διαδικασίας παραγωγής και την ευελιξία στη διαμόρφωση κάθε οχήματος χωριστά της Hyundai (2017), τον έλεγχο της παραγωγής μέσω της ανάλυσης ήχου με τη βοήθεια τεχνητής νοημοσύνης που χρησιμοποιεί η Skoda, το ευφυές σύστημα διαχείρισης ενέργειας (iEMDS) που διαθέτουν τα εργοστάσια του BMW Group, μεταξύ άλλων.
Τι ακριβώς είναι το Industry 4.0;
Με τον όρο “Industry 4.0” εννοούμε την Τέταρτη Βιομηχανική επανάσταση που ορίζεται ως ένα νέο επίπεδο οργάνωσης και ελέγχου σε ολόκληρη την αλυσίδα αξίας του κύκλου ζωής των προϊόντων. Αν μπείτε στη διαδικασία να αναζητήσετε διευκρινίσεις, στη σχετική βιβλιογραφία μπορείτε να δείτε ότι το “Industry 4.0” επιδιώκει να μετατρέψει τις «κανονικές» μηχανές σε μηχανές οι οποίες θα έχουν τη δυνατότητα να μαθαίνουν (“self-learning machines”) με στόχο, όπως είναι φυσικό, τη βελτίωση τόσο της συνολικής τους απόδοσης, όσο και της διαχείρισης της αλληλεπίδρασης με το περιβάλλον. Το “Industry 4.0” στοχεύει επίσης στην κατασκευή μιας ανοιχτής, ευφυούς πλατφόρμας παραγωγής για εφαρμογές βιομηχανικών δικτύων. Στο πλαίσιο αυτό, για να «δουλέψει» το “Industry 4.0” απαραίτητη είναι η παρακολούθηση δεδομένων σε πραγματικό χρόνο, η παρακολούθηση της κατάστασης και της θέσης του προϊόντος, καθώς και η διαχείριση των οδηγιών για έλεγχο των διαδικασιών παραγωγής.
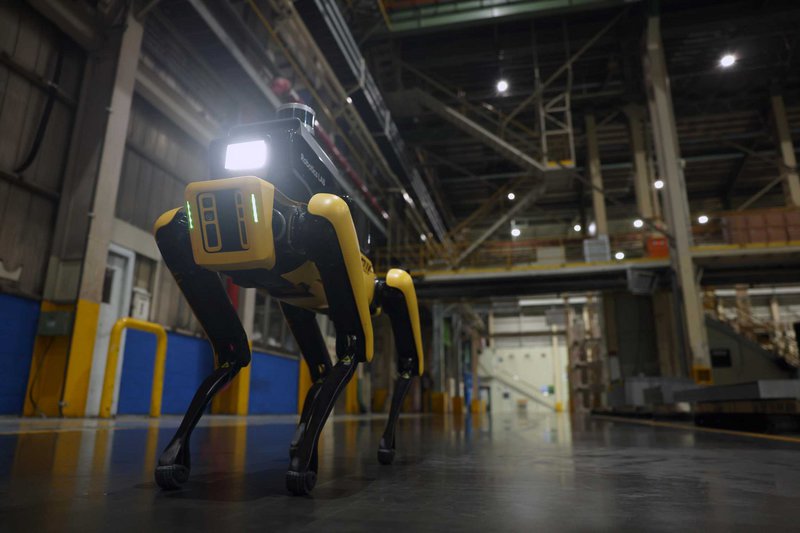
Το “Industry 4.0” προέκυψε από την ανάγκη αυτού που πολύ συχνά θα ακούσετε να αποκαλείται «εξατομίκευση» – και είναι αυτό κάτι με το οποίο στον χώρο του αυτοκινήτου ερχόμαστε πολύ συχνά σε επαφή. Το 3-D Printing, με το οποίο είχαμε ασχοληθεί σε προηγούμενο άρθρο μας, έρχεται να καλύψει ένα μέρος της ανάγκης αυτής, ωστόσο το ζήτημα της εξατομίκευσης είναι πολύ πιο ευρύ όταν μιλάμε για μαζική παραγωγή και για απαιτήσεις πελατών-εταιριών που δεν αγοράζουν, βέβαια, ούτε ένα ούτε δύο, ούτε τρία, αλλά δεκάδες ή και εκατοντάδες χιλιάδες «κομμάτια» από κάθε είδος.
_77761_436111_type15016.jpg)
Με βάση αυτές τις απαιτήσεις προέκυψαν οι τέσσερις βασικοί άξονες του ‘’Industry 4.0’’: πρόκειται για το Internet of Things (IoT), το Industrial Internet of Things (IIoT), τη βασισμένη στο «σύννεφο» παραγωγή (“Cloud based Manufacturing”), καθώς και την «έξυπνη» παραγωγή (“Smart Manufacturing”) που βοηθά στη μετεξέλιξη της παραγωγικής διαδικασίας σε πλήρως ψηφιοποιημένη και ευφυή. Και αν θέλουμε να αναλύσουμε περαιτέρω, αλλά και να κάνουμε πιο κατανοητές τις παραπάνω έννοιες διερευνώντας τι αντιστοιχεί στους άξονες αυτούς, θα πρέπει να μιλήσουμε για τους εννέα πυλώνες του “Industry 4.0”, που δεν είναι άλλοι από:
_77761_436112_type15016.jpg)
1. Το διαδίκτυο των πραγμάτων – Internet of Things (IoT)· 2. Τη χρήση δικτυωμένων υπολογιστών για ανάλυση και επεξεργασία δεδομένων (“Cloud Computing”)· 3. Τα αυτόνομα ρομποτικά συστήματα (“Autonomous Robots”)· 4. Την ανάλυση μεγάλων δεδομένων (“Big Data”)· 5. Την επαυξημένη πραγματικότητα (“Augmented Reality”)· 6. Την ασφάλεια στον κυβερνοχώρο (“Cyber Security”)· 7. Την προσομοίωση (“Simulation”)· 8. Την ενοποίηση συστημάτων (“System Integration”) και 9. Tην προσθετική κατασκευή (“Additive Manufacturing/3-D printing”).
Οι παραπάνω όροι μπορεί να μοιάζουν βγαλμένοι από ταινία επιστημονικής φαντασία ή, στην καλύτερη περίπτωση, από κάποια επιστημονική εργασία, πρόκειται, όμως, για απολύτως ρεαλιστικές έννοιες και διαδικασίες που ήδη «τρέχουν» στο πλαίσιο της υπό εξέλιξης Τέταρτης Βιομηχανικής επανάστασης, της οποίας τυγχάνουμε μάρτυρες. Το “Industry 4.0” προωθεί τη σύνδεση φυσικών στοιχείων, όπως αισθητήρες, συσκευές και άλλα εργαλεία που χρησιμοποιεί μια βιομηχανίας μεταξύ τους, αλλά και τη σύνδεση όλων μαζί με το διαδίκτυο. Κάπως έτσι φτάνουμε στα λεγόμενα “Cyber Physical Systems”, όπου έχουμε μια άμεση σύνδεση μεταξύ ψηφιακού και φυσικού/πραγματικού κόσμου
Βασική διαφορά δε του “Industry 4.0” σε σχέση με τον «απλό» έλεγχο της παραγωγής μέσω υπολογιστών (Computer Integrated Manufacturing - CIM) είναι η ενσωμάτωση του ανθρώπου στην παραγωγική διαδικασία, έτσι ώστε να υπάρχει συνεχής βελτίωσή της, εστίαση σε δραστηριότητες προστιθέμενης αξίας, καθώς και εξοικονόμηση πρώτων υλών, ενέργειας κ.λπ. Ας δούμε, όμως, πώς υλοποιούνται στην πράξη όλα αυτά από τη σύγχρονη αυτοκινητοβιομηχανία, με συγκεκριμένα παραδείγματα.
BMW Google Glass
Σε μια αυτοκινητοβιομηχανία, στο πλαίσιο του ελέγχου της παραγωγής, απαιτούνται 10 έως 25 ανεξάρτητες δοκιμές για ένα όχημα, ανάλογα με τον εξοπλισμό του. Για την τεκμηρίωσή τους, οι αρμόδιοι ελεγκτές έπρεπε παλιότερα να πηγαινοέρχονται μεταξύ αυτοκινήτου και υπολογιστή, υποβάλλοντας γραπτές αναφορές που πολλές φορές ήταν ασαφείς, με αποτέλεσμα να προκύπτουν πρόσθετα ερωτήματα από το υπεύθυνο τμήμα στο 25% των περιπτώσεων. Με τα έξυπνα γυαλιά που εισήγαγε το 2014 η BMW στο εργοστάσιο του Σπάρτανμπουργκ, το προσωπικό του κέντρου ανάλυσης μπορεί τώρα να προσθέτει φωτογραφίες και βίντεο στις αναφορές του. Η οθόνη κεφαλής περιλαμβάνει κάμερα με τρεις διαφορετικές ρυθμίσεις: λήψη φωτογραφίας, εγγραφή βίντεο και background βίντεο. Χάρη στα Google Glass, το προσωπικό δοκιμών παραμένει στο όχημα, βλέπει τα σχέδια δοκιμών στην ενσωματωμένη οθόνη της συσκευής και τα εγκρίνει μέσω φωνητικού ελέγχου.
Ανάλυση ήχου από τη Skoda

Παρόμοια με την ανάλυση εικόνας, η ανάλυση ήχου είναι κάπως πιο απλή. Βασίζεται στο γεγονός ότι κάθε μηχανή εκπέμπει χαρακτηριστικούς ήχους που μπορούν να μελετηθούν από την Τεχνητή Νοημοσύνη (“Artificial Intelligence” – AI). Όταν ανιχνευθεί ένας νέος ήχος, αυτό κατά πάσαν πιθανότητα σημαίνει ότι κάτι δεν πάει καλά. Η παρέμβαση της ΑΙ είναι αυτή που καθιστά δυνατή την ανίχνευση πιθανών βλαβών προτού προκαλέσουν οποιαδήποτε ζημιά. Για παράδειγμα, όταν ένα ρουλεμάν αρχίσει να χάνει τις ιδιότητές του και δεν προσφέρει την απαιτούμενη, μέσω της ολίσθησης, μείωση της τριβής ή όταν ένα γρανάζι, ένας ιμάντας ή μια αλυσίδα βρίσκεται σε κάποιο αρχικό στάδιο φθοράς, ο ήχος διαφοροποιείται. Αυτό ένας άνθρωπος δεν μπορεί να το αντιληφθεί με «το αυτί», αλλά η AI μπορεί. Τα υπόλοιπα είναι θέμα παρέμβασης των τεχνικών που αντικαθιστούν το αντίστοιχο εξάρτημα αποτρέποντας την εμφάνιση κάποιας δυσλειτουργίας ή βλάβης.
Οι ευφυείς μετρητές ενέργειας του BMW Group
_77761_436123_type15016.jpg)
Ένα ευφυές σύστημα διαχείρισης δεδομένων ενέργειας με την ονομασία iEDMS (“Intelligent Energy Management Data System”) χρησιμοποιεί, ήδη από το 2012, το BMW Group σε μια σειρά εργοστάσιά του: Σπάρτανμπουργκ (Νότια Καρολίνα, ΗΠΑ), Λειψία, Ρέγκενσμπουργκ, Μόναχο και Λάντσουτ κ.λπ. Το σύστημα αυτό βασίζεται σε ευφυείς μετρητές (ρολόγια) ηλεκτρικής ενέργειας που μετρούν συνεχώς την κατανάλωση σε διάφορα τμήματα των εγκαταστάσεων (ρομπότ κ.λπ.) και είναι ενσωματωμένοι στα υπάρχοντα συστήματα που καταγράφουν την κατανάλωση ενέργειας.
Από την πρώτη χρονιά της λειτουργίας του iEDMS, στο εργοστάσιο του Σπάρτανμπουργκ, είχαν εφοδιαστεί με έξυπνους μετρητές πάνω από 80 μηχανήματα παραγωγής και ρομπότ. Αξίζει να σημειωθεί ότι μέσα σε λίγες μόλις εβδομάδες από την τοποθέτηση τους, εξοικονομήθηκε μέχρι και το ένα τέταρτο του κόστους ενέργειας σε διάφορα στάδια της παραγωγής. Αυτό έγινε κατορθωτό ποικιλοτρόπως: για παράδειγμα, συγκρίνοντας τρία δυναμόμετρα εφάμιλλων προδιαγραφών, αποδείχτηκε ότι ένα από αυτά απαιτούσε σχεδόν διπλάσια ηλεκτρική ενέργεια ανά δοκιμαζόμενο όχημα σε σχέση με τα άλλα δύο. Αιτία ήταν ένα σφάλμα του προγράμματος στη διαχείριση του χρόνου λειτουργίας του εξαερισμού. Σε συνδυασμό με περαιτέρω δράσεις βελτιστοποίησης, η συνεχής παρακολούθηση των τριών μηχανημάτων μέσω iEMDS είχε ως αποτέλεσμα να εξοικονομηθούν συνολικά περισσότερα από 100 MWh (100.000 κιλοβατώρες) την πρώτη χρονιά.
Μέχρι το 2013, η εταιρεία κατάφερε να μειώσει την κατανάλωση ενέργειας κατά 31%, ενώ μέχρι το 2020 η κατανάλωση ενέργειας ανά παραγόμενο όχημα μειώθηκε σε ποσοστό 45% σε σχέση με τα επίπεδα του 2006.
Smart Factory Technology από τη Hyundai
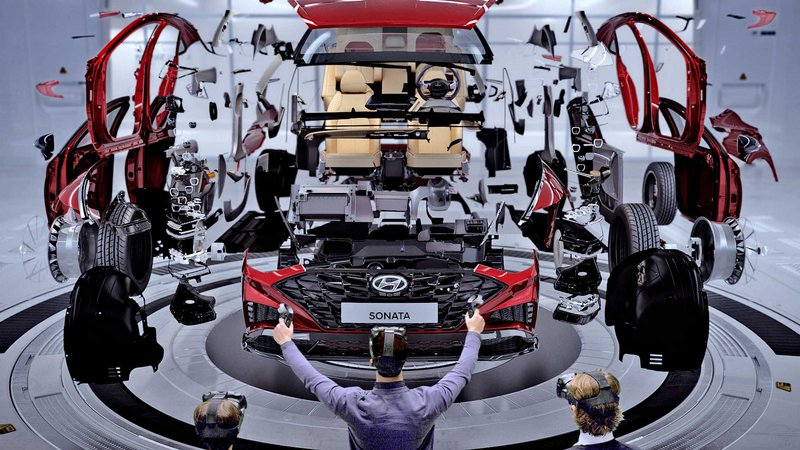
Τον Ιούνιο του 2017, το Hyundai Motor Group παρουσίασε το Smart Tag System (σύστημα ευφυούς ετικέτας), που αποτελείται από ένα αισθητήρα εντοπισμού θέσης με μνήμη υψηλής χωρητικότητας και τσιπ ασύρματης επικοινωνίας. Χάρη σε αυτό το σύστημα, κάθε αυτοκίνητο σε μια γραμμή συναρμολόγησης επισημαίνεται με μια μικρή «έξυπνη» ετικέτα, έτσι ώστε το ρομπότ συναρμολόγησης να μπορεί να αναγνωρίσει το μοντέλο που κατασκευάζεται και να διαφοροποιήσει τη συναρμολόγηση σύμφωνα με τις προδιαγραφές του μοντέλου. Καθώς είναι αρκετά συνηθισμένο να συναρμολογούνται πολλά μοντέλα σε μια ενιαία γραμμή συναρμολόγησης σε περιόδους υψηλής ζήτησης, το σύστημα επιτρέπει την απρόσκοπτη διαχείριση πολλών μοντέλων, διατηρώντας, παράλληλα, χαμηλά τα ποσοστά τυχόν ελαττωμάτων.
Οι «ευφυείς» τεχνολογίες δεν περιορίζονται, όμως, μόνο στην κατασκευή, αλλά βρίσκουν εφαρμογή και στη σχεδίαση. Η διαδικασία σχεδίασης εικονικού οχήματος που παρουσίασαν οι Κορεάτες τον Δεκέμβριο του 2019 αξιοποιεί την τεχνολογία της εικονικής πραγματικότητας VR (“Virtual Reality”), η οποία επιτρέπει την προσομοίωση του μοντέλου αυτοκινήτου και του περιβάλλοντος οδήγησης σε μια εικονική σφαίρα. Στη συνέχεια, οι ψηφιακές προσομοιώσεις διευκολύνουν τους ελέγχους σχεδίασης/κατασκευής, καθώς και τη διασφάλιση ασφάλειας/ποιότητας, παρέχοντας στους μηχανικούς ευελιξία στην πραγματοποίηση γρήγορων προσαρμογών.
Ενάμιση περίπου χρόνο πριν, τον Μάρτιο του 2018, το Hyundai Motor Group είχε ανοίξει τη μεγαλύτερη μονάδα αξιολόγησης σχεδίασης με τη βοήθεια VR στον κόσμο, που μπορεί να φιλοξενεί ταυτόχρονα 20 άτομα σε ένα ενιαίο εικονικό περιβάλλον. Σε αυτή την εγκατάσταση εικονικής πραγματικότητας, οι μηχανικοί μπορούν να δουν το εικονικό μοντέλο μέσα και έξω σαν να ήταν ένα πραγματικό αυτοκίνητο, περιστρέφοντάς το ή/και αλλάζοντας τον φωτισμό ανάλογα με τις ανάγκες.
Τα «εικονικά» εργοστάσια του Renault Group
_77761_436113_type15016.jpg)
Στο “Metaverse” (μετασύμπαν) του Renault Group, φιλοξενείται ένα πραγματικό αντίγραφο του αληθινού κόσμου, που ελέγχεται σε πραγματικό χρόνο. Κάθε μέρα, στις βιομηχανικές εγκαταστάσεις του Renault Group συλλέγονται ένα δισεκατομμύριο δεδομένα. Το 100% των γραμμών παραγωγής της γαλλικής εταιρείας συνδέονται μεταξύ τους (8,500 μηχανές και λοιπός εξοπλισμός), ενώ παρακολουθείται –σε μόνιμη βάση– το 90% των εφοδιαστικών ροών και το 100% των δεδομένων της εφοδιαστικής αλυσίδας. Το Metaverse παρέχει, λοιπόν, τη δυνατότητα του άμεσου ελέγχου, γεγονός που αυξάνει την ευελιξία και την προσαρμοστικότητα των βιομηχανικών λειτουργιών.
Για τη συλλογή δεδομένων από όλες τις βιομηχανικές του εγκαταστάσεις, το Renault Group έχει αναπτύξει μια μοναδική εφαρμογή μαζικής συλλογής και τυποποίησης δεδομένων μοντελοποιώντας τα φυσικά περιουσιακά του στοιχεία σε ψηφιακούς κλώνους (“Digital Twins”). Κάθε εργοστάσιο έχει το τον δίδυμο αδελφό του, ένα πιστό αντίγραφό του στον εικονικό κόσμο, ενώ κάτι αντίστοιχο συμβαίνει και με την εφοδιαστική αλυσίδα, αποτελώντας αναπόσπαστο μέρος του “Metaverse”, ενώ ελέγχεται και αυτή σε πραγματικό χρόνο, από το κέντρο ελέγχου του συστήματος.
_77761_436115_type15016.jpg)
Οι ψηφιακοί κλώνοι εμπλουτίζονται με δεδομένα από τους προμηθευτές, τις προβλέψεις των πωλήσεων, αλλά και πέραν της παραγωγής πληροφορίες, όπως ο καιρός, η κίνηση στους δρόμους κ.λπ. – με την Τεχνητή Νοημοσύνη να επιτρέπει την ανάπτυξη σεναρίων πρόγνωσης. Η δημιουργία αυτού του ψηφιακού σύμπαντος έγινε εφικτή μέσω της αξιοποίησης διαφόρων τεχνολογιών (“Cloud”, “Real Time”, 3-D, “Big Data”...), με τους αλγόριθμους της Tεχνητής Νοημοσύνης (AI) να διευκολύνουν τους εργαζομένους να κάνουν τις αντίστοιχες προβλέψεις, προβαίνοντας στις αντίστοιχες διορθωτικές κινήσεις όταν και όπου χρειάζεται. Σημειώστε ότι από το 2019, έχουν πραγματοποιηθεί 300 «συναγερμοί», και έχουν αποτραπεί ισάριθμες διακοπές της παραγωγής.
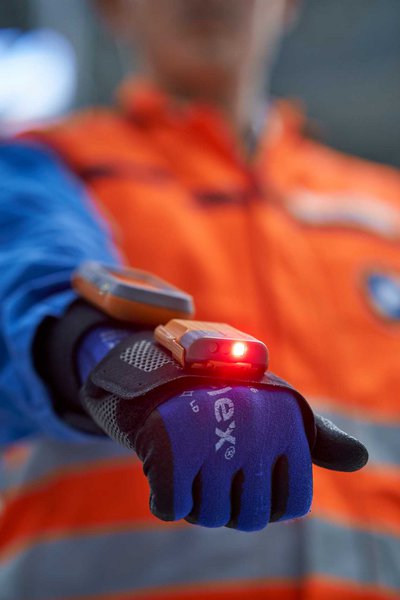
Κάνοντας, λοιπόν, πράξη την τέταρτη βιομηχανική επανάσταση, η Renault υπολογίζει το όφελός της από το 2016 μέχρι σήμερα 780 εκ. ευρώ, ενώ ως το 2025 σε αυτά θα προστεθούν ακόμα 320 εκ. ευρώ, καθώς και άλλα 260 εκ. ευρώ που θα προκύψουν λόγω εξοικονόμησης από τον τομέα των αποθεμάτων, αλλά και από την κατά 60% μείωση των χρόνων παράδοσης κάθε αυτοκινήτου και την κατά 50% μείωση του ανθρακικού αποτυπώματος της παραγωγής του.
Οι τέσσερις βιομηχανικές επαναστάσεις
Πρώτη Βιομηχανική επανάσταση (1784)
Εκμηχάνιση της παραγωγής με τη βοήθεια της δύναμης του νερού και των ατμομηχανών,
Δεύτερη Βιομηχανική επανάσταση (1870)
Μαζική παραγωγή με τη βοήθεια του εξηλεκτρισμού.
Τρίτη Βιομηχανική επανάσταση (1970)
Αυτοματοποίηση της παραγωγής με τη βοήθεια των PLC (“Programmable Logic Controller”)
και της πληροφορικής (IT – “Information technology”).
Τέταρτη Βιομηχανική επανάσταση (Σήμερα)
Σύνδεση ψηφιακού και φυσικού κόσμου με τη βοήθεια του IoT (“Internet of Things”)
και των CPS (“Cyber Physical Systems”).